Glass Bottle Manufacturing is a critical industry that produces bottles used for packaging a variety of products such as food, beverages, and pharmaceuticals.
Glass bottles have been a preferred packaging option for many years due to their durability, versatility, and eco-friendliness. However, with increasing competition and production costs, manufacturers must find ways to optimize their operations to remain competitive. Maximizing efficiency is key to achieving this goal and requires a combination of modern equipment, optimized production processes, quality control systems, employee training, and a focus on sustainability.
The glass bottle manufacturing industry is constantly evolving, and manufacturers must stay up to date with the latest technologies and best practices to remain competitive. In this article, we will explore some tips and tricks for glass bottle manufacturers to maximize their efficiency and improve their bottom line.
Page Contents
Invest in modern equipment
One of the most effective ways to increase efficiency is to invest in modern equipment. Newer machines are more efficient, and faster, and often have better automation and control systems. Upgrading equipment can reduce downtime, increase production speeds, and improve product quality. Investing in modern equipment also helps to reduce maintenance costs, minimize energy consumption, and improve safety.
Optimize production processes
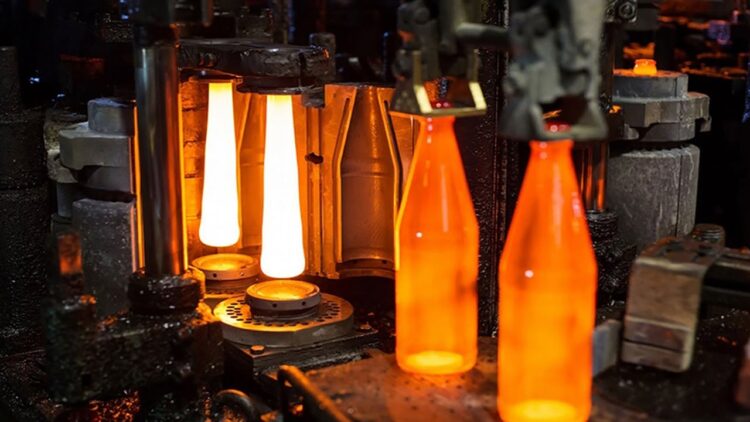
Source: ceramicninja.com
Efficient production processes are critical to maximizing output and reducing costs. Analyzing and optimizing the production process can help identify areas where bottlenecks occur or where there is room for improvement. Techniques such as lean manufacturing can help streamline production, eliminate waste, and improve quality. Automation can also help reduce human error and speed up production.
Implement a quality control system
Implementing a quality control system is critical for ensuring consistent quality in glass bottle manufacturing. By establishing standard procedures and protocols for checking and testing the quality of glass bottles, manufacturers can identify potential defects early and prevent further issues down the line. A quality control system can also help to catch defects before they reach the customer, improving customer satisfaction and reducing the risk of costly recalls. Investing in a quality control system can help to ensure that only high-quality bottles are shipped to customers, leading to better overall business performance and a positive reputation in the industry.
Train employees
Proper training is essential for ensuring that employees understand the production process and can operate the equipment effectively. Providing regular training and development programs can help employees acquire new skills and knowledge, reducing the likelihood of mistakes and accidents. Investing in employee training can also improve morale, productivity, and retention rates.
Focus on sustainability
Sustainability is increasingly becoming a priority for consumers, and glass bottle manufacturers can benefit by focusing on sustainable practices. Improving energy efficiency, reducing waste, and using recycled materials are all ways to reduce the environmental impact of glass bottle manufacturing. Sustainability practices can also help companies save money by reducing energy costs and minimizing waste.
Conclusion
In conclusion, maximizing efficiency in glass bottle manufacturing requires a combination of strategies, including investing in modern equipment, optimizing production processes, implementing quality control systems, training employees, and focusing on sustainability. By following these tips and tricks, glass bottle manufacturers can reduce costs, increase output, and improve their bottom line.
Read also this article.