From the plastic bottles holding your morning orange juice to the synthetic fibres woven into your favourite sweater — polyolefins impact our everyday lives. This category of versatile plastic materials derives from simple olefin compounds and makes up over 50% of the 300 million tonnes of plastics produced globally each year.
Known for their rugged durability, polyolefins also tout water, chemicals, and heat resistance. Their customised properties lend well to creating the shrink-wrap around your online purchase orders and the tough piping funnelling water into your home. Even the soft foam padding of your new trainers likely came from polyolefin stock.
Yet despite their ubiquity across UK kitchens, construction sites, and car engines, polyolefins remain uncelebrated workhorses of industry and consumers alike. This guide covers everything you need to know about polyolefin.
Page Contents [show]
Introduction to Polyolefins
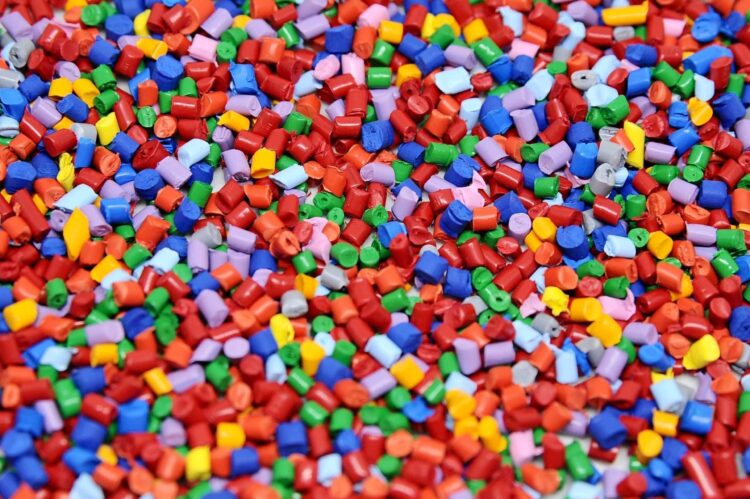
Source: plasticseurope.org
Polyolefins refer to the family of plastics derived from polymers of simple olefin monomers like ethylene and propylene. Their properties range widely from flexible and ductile plastics to rigid, crystalline polymers. Thanks to their affordability and versatility, polyolefins now constitute over half of total plastic production globally as well as within the UK. They continue growing in ubiquity across British manufacturing.
Common Types of Polyolefins
Polyethylene represents the most produced polyolefin globally and in the UK. Variants like low-density polyethylene (LDPE) and linear low-density polyethene (LLDPE) offer affordability, processability and flexibility suited for plastic bags and film packaging, available from a range of shrink film suppliers. High-density polyethylene (HDPE) provides greater stiffness and chemical resistance leveraged in plastic bottles and chemical tanks
After polyethylene, polypropylene holds the second largest market share of polyolefins used in the UK. With higher melting points but lower density than polyethene, polypropylene brings useful thermal stability, chemical resistance and rigidity to products ranging from carpeting and auto parts to food containers and dishware.
While less common, speciality polyolefins like polybutene and polymethylpentene fill niche needs for lubricant manufacturing and electronics, respectively.
Polyolefin Manufacturing
Industrial production of polyolefins relies on the polymerization of olefin gases in the presence of metal-based catalysts. Common catalytic systems include Ziegler-Natta, Chromium-based Phillips, and metallocene catalysts. Introduction of these highly reactive catalysts accelerates the olefin polymerization reaction — often making it violently exothermic. Tight control over processing conditions like temperature, pressure and additive levels allows manufacturers to tailor end-product properties like molecular weight distribution and branching levels. Varying the processing aids in shaping polyolefin crystallinity, melt behaviour, flexibility and durability to meet application needs.
Key Properties and Applications of Polyolefin
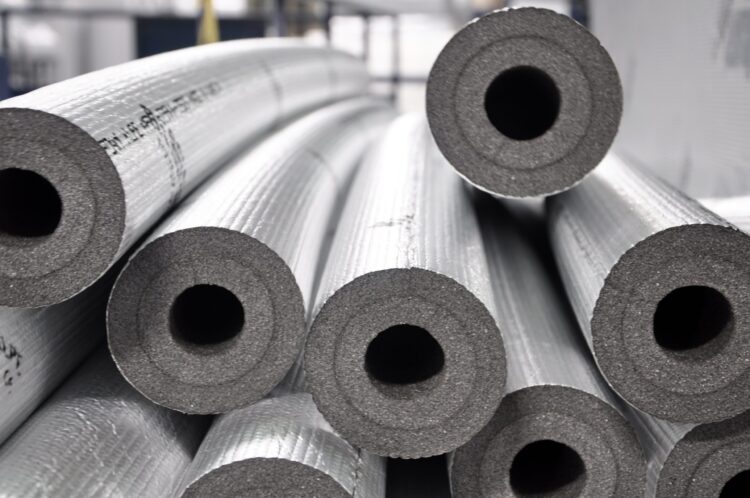
Source: aerofoamusa.com
Mechanical Properties
The mechanical integrity of polyolefins spans a wide spectrum — from viscous liquids to stiff, rugged plastics. This diversity stems from the relative influences of molecular weight and degree of crystallinity. While low crystal content provides ductile, flexible materials, higher crystallinity drives rigid and brittle consistencies. Polymer variants producing intermediate, semi-crystalline forms enable better impact resistance. Manipulating these molecular traits allows manufacturers to tailor mechanical performance.
Chemical Properties
One prime advantage of polyolefins is chemical stability and solvent resistance. With non-reactive carbon-carbon backbones, these plastics withstand exposure to acids, bases, oils and other chemicals without degrading. This durability makes them indispensable for containing corrosive substances. However, the chemical resistance also makes welding polyolefins together challenging without special surface treatments.
Thermal Properties
In addition to chemical stability, polyolefins offer thermal stability across a wide temperature range — especially varieties like polypropylene designed for higher melting points. This helps their usefulness as lubricants, in hot-fluid pipes and automotive parts enduring engine heat. More specialized “heat-shrink” polymer variants take advantage of thermally-triggered contraction for self-sealing insulation across junctions.
Major Uses in UK
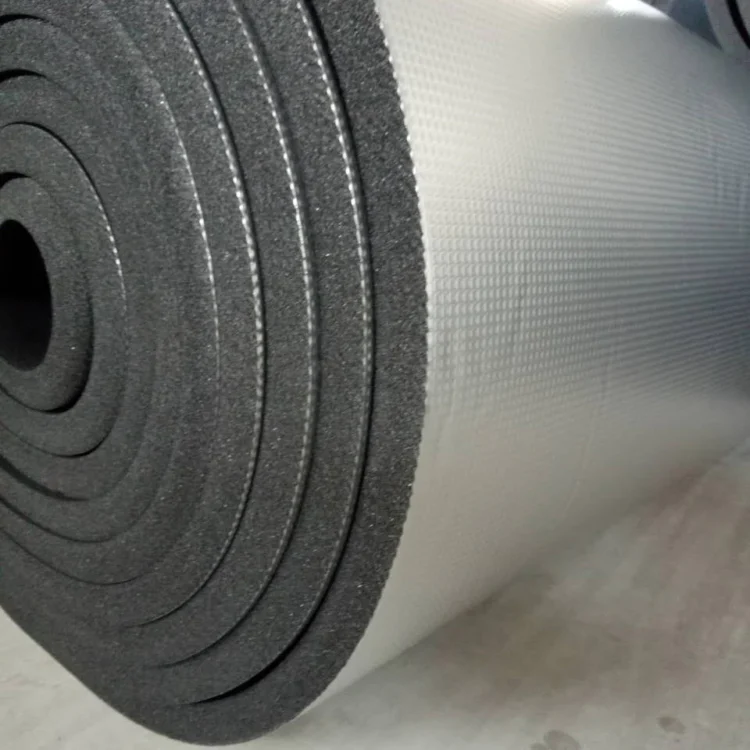
Source: ritemore.com
Exported across over 100 countries, UK polyolefin producers supply materials for packaging, construction, automotive, electronics and consumer industries. Polyethene and polypropylene comprise over 70% of plastics demanded within the UK for ubiquitous applications like films, containers, pipes and parts enduring rugged, outdoor or high-heat conditions. As needs for affordability, chemical resistance and heat tolerance grow across British manufacturing sectors, so too does reliance on these versatile, homegrown polyolefins.
Conclusion
While often unseen, polyolefins impact your life daily – whether in your fruit’s packaging, your car’s moulded bumper or the durable fibres weaving your outfit. Behind the mundane visibility though lies materials science at its best – tailored chemistry and precision processing unlocking affordable products to meet society’s needs.
Here in the UK, homegrown polyolefin producers pioneer advances in mechanical flexibility, thermal capability and chemical resistance to power innovation across sectors like construction, automotive, electronics and more. The quest does not end either. With increasing awareness around plastic waste and recycling, researchers push new frontiers in designing durable yet degradable polyolefin variants using renewable inputs.
In these ways, the applications benefiting from polyolefins continue expanding as quickly as the industry can keep up. Far from the perceived commodities of decades past, these versatile plastics form a cornerstone of technical materials advancing UK enterprise. Just remember the hidden capabilities underpinning your everyday routines as you drink that next sip of orange juice or tie up your durable trainers. Polyolefins may remain silently working in the background, but they build the platforms that enable consumers and industries alike to reach
the next level.