A lot of businesses need inclined conveyors to quickly and easily move things uphill. But if you don’t have the right safety gear, you could crash, get hurt, or even die. To keep workers safe and things running smoothly, it’s important to follow strict safety rules. In this blog post, we’ll talk about some important safety steps for using an incline conveyor.
Page Contents
Full-Service Training
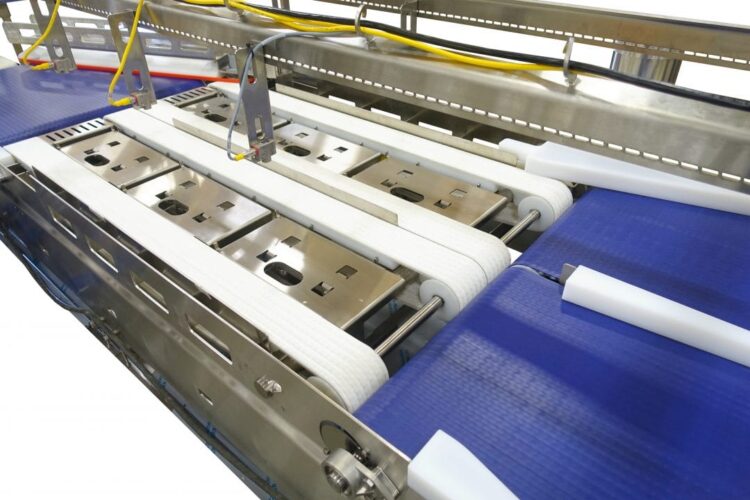
Source: dornerconveyors.com
Workers have to learn a lot about how to use an incline conveyor, keep it safe, and what to do in an emergency before they can use it. To be trained, people need to know how to use the tools, spot possible dangers, and act in a situation. People should be able to take regular safety lessons to help them remember what they know.
Monthly Checks and Maintenance
To keep incline conveyors working at their best, they need to be checked and fixed up regularly. Check all the parts, like the supports, belts, pulleys, rollers, and pulleys, for signs of damage, wear, or tear. Any issues that are found must be fixed right away to keep tools from breaking and causing accidents.
Guards and Covers
People shouldn’t be able to reach the moving parts of inclined conveyors, so they should have the right guards and covers on them. Sticky guards should be put up around nip points, pinch points, and other dangerous spots. Also, when the gates and entry doors are opened, they need to be interlocked so that the conveyor stops moving.
Emergency Stop Systems
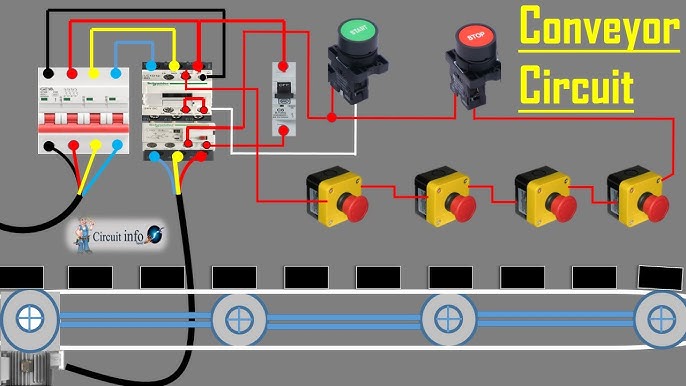
Source: youtube.com
The emergency stop systems are very important because they let you stop the conveyor quickly in an emergency or when something is unsafe. An emergency stop button should be put along the conveyor belt so that it is easy for workers to reach. Making sure that emergency stop devices work well when they’re needed means testing them often.
Correct Ways to Load and Unload
For safe conveyor operations, the correct ways to load and unload are necessary. If you put too much on the conveyor, it can break and cause more crashes. Workers should be taught how to evenly distribute loads and safely fasten them so they don’t move around while they’re being moved.
Personal safety equipment (PPE)
To reduce risks, workers who are near or working with incline conveyors must wear the right PPE. This could include hard hats, protection eyewear, safety gloves, steel-toed boots, and clothing that stands out. Making sure that workers always wear PPE greatly lowers the chance of them getting hurt.
Safety Signage and Communication
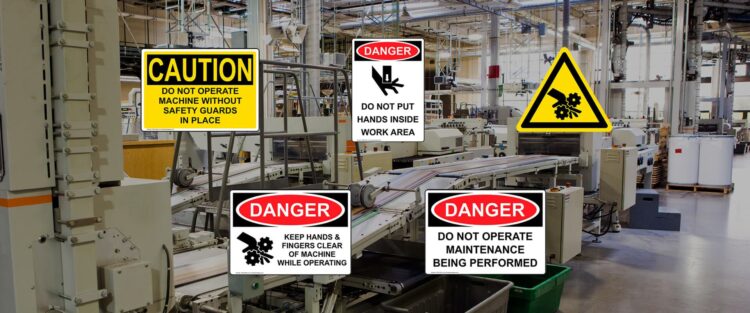
Source: prismont.com
Along the conveyor path, there should be clear and visible safety signs that warn workers of possible dangers and give them safety instructions. Also, good communication systems, like alarms, signals, or two-way radios, let operators and staff talk to each other quickly in case of situations or changes to the way things are done.
Safety reviews and audits on a regular basis
Doing safety checks and reviews on a regular basis helps find places to improve and makes sure that safety rules are followed. During these checks, equipment should be checked, safety rules should be followed, and workers should be asked for feedback on safety concerns or ideas for improvements.
Inclined conveyors are essential to many different types of businesses, but they pose risks that necessitate strict safety measures. Employers can make the workplace safer and stop accidents by putting an emphasis on thorough training, regular checks, proper guarding, emergency stop systems, and other safety procedures. Keep in mind that safety should always come first when using an incline conveyor to protect both workers and output.
With these important safety measures in place, you can stay safe, stay informed, and keep things running smoothly.