Magnetic flux leakage testing is a nondestructive testing technique in pipeline inspection. It uses magnetic sensors in the detection of defects on internal and external surfaces of the pipelines. At this article here, you can learn more about this technology. MFL testing is a popular in-line inspection technique. Alternative testing techniques are;
- Eddy current inspection
- Ultrasonic inspections
- Ray inspection
- Penetration inspection technique
The most popular pipeline inspection techniques are Magnetic flux leakage and Ultrasonic inspection. But for more analysis and evaluation, other methods may apply. Through the use of magnetic powder, the sensors display results as piles. Most operators prefer this method because of its high sensitivity, intuitiveness, and simplicity too. There are many developments in semiconductor electronics. That has helped in improving the efficiency and effectiveness of the Magnetic Flux Leakage testing technique.
Reasons for Pipeline defect detection are as follows;
- Safety precautions
A pipeline system is the safest way to transport oil or gas. And in most cases, the pipelines are buried underground. They are prone to corrosion or deformation and other defects due to humidity and pressure. Testing for such defects may help prevent leakages or fatalities.
- Advanced pipeline technology and operation procedures
Previous pipeline technology requires maintenance and upgrade to the latest technology. Regular inspection through modern MFL or PIG testing techniques can help identify the gaps. Repairing or replacing the pipelines made using the latest technology can help to bring down maintenance costs. The in-line inspection also becomes easy.
- Maintain pipeline integrity
Pipeline integrity maintenance helps in preventing depreciation rates. It also ensures that one complies with the set rules and regulations in the oil and gas transportation industry. The pipeline inspection team should monitor susceptibility to cracks and corrosion of the pipelines.
Page Contents
Advantages of MFL testing technique
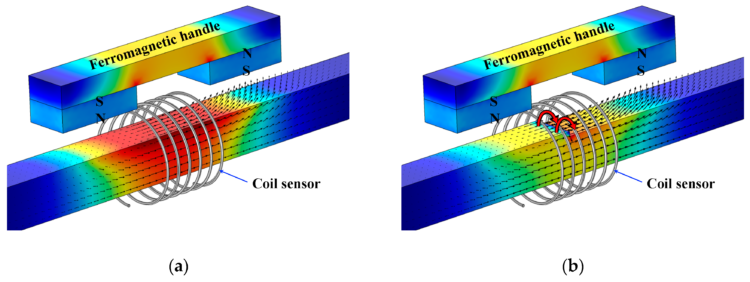
Source: mdpi.com
- It can detect cracks and dents on circumferential and axial directions
- No need to pre-process
- Easy signal detection
- Compatible with online detection and easy to implement automation
- Many defects such as scars, shrinkage cavities, corrosion, and pitting detection
- Low detection environment requirements
- Transportation does not affect detection environment requirements for MFL
Limitations of MFL testing
- Complete magnetic field saturation is a must
- Impurities in the pipeline materials may give wrong data
- Restriction in long and axial narrow defect detection
- High sensitivity high-speed vehicles
MFL testing previously was all about qualitative defect identification. But nowadays, it gives quantitative analysis that operators can use to implement new pipeline maintenance procedures to help maintain the set standards in the oil and gas industry.
Magnetic field measuring methods
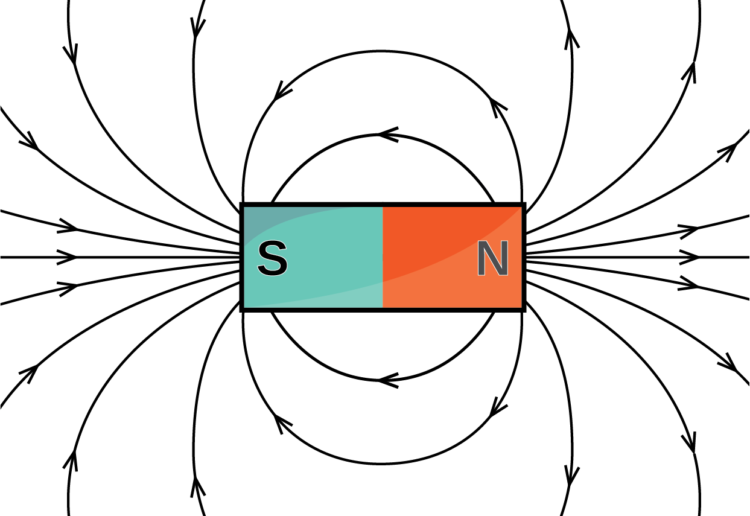
Source: bitescis.org
There are many methods used to measure the magnetic field. For more accuracy, there must also be high strength magnetization to achieve high saturation. Here are some of the methods for measuring the magnetic field. Advancement in computer technology, the development of sensors, and electronic technology contribute to the high accuracy in measurements using the MFL testing technique.
1. Electromagnetic induction
Based on Faraday’s law relating to electromagnetic induction, magnetic fields, through measuring instruments such as induction coils, electronic integrators, and magnetic flux meters, they can measure magnetic field intensity in DC, pulsed, and AC.
2. Hall effect
The magnetic PIG that has a Hall sensor can measure the electromotive force that the electric current generates. The approach offers more stability and measures temperature characteristics more effectively. For more accuracy, more Hall elements should be in an array. That way, it can also prevent undetected flaws and also control the resolution.
3. Magnetic resistance method
U ferromagnetic thin film or semiconductor reluctance elements, one can measure changing characteristics in the magnetic field. Such effects analysis can help in identifying any defects during the inspection. Encapsulating the hall element helps to angle deflection and vibration. That also strengthens the circuit connection and enhances the accuracy and detection sensitivity.
4. Magneto-optical effects
In harsh environments, this method is most suitable. Through its optical fiber sensors, it can detect and transmit data for analysis. It also uses the approach of magneto-optical effects in capturing data.
5. Resonance imaging technique
Here, various types of devices measure resonance. An electromagnetic wave generates particles in the magnetic field that produce a resonance. The resonance differs depending on the magnetic field environment. The commonly used device for measuring resonance is magnetometers. Depending on the inspection process, one may use the nuclear magnetic resonance with higher precision and the electro spin magnetometer.
The sensor may be magnetic or not. Non Magnetic sensors are not as effective as magnetic ones. They include temperature sensors, odometer detectors, hydraulic or pneumatic pressure sensors, and differential pressure sensors. There are many types of magnetic sensors. Their role is to convert magnetic signals to electrical signals for easy analysis. Some of the magnetic sensors are:
- Induction coils.
- Flux gates
- Transistors and diodes
- Magnetic resistances
- Hall components
Service providers should choose the most appropriate sensor since they vary in intensity. For high-intensity sensitivity, most pipeline inspection experts use magnetic resistance.
MFL analysis and use in pipeline inspection
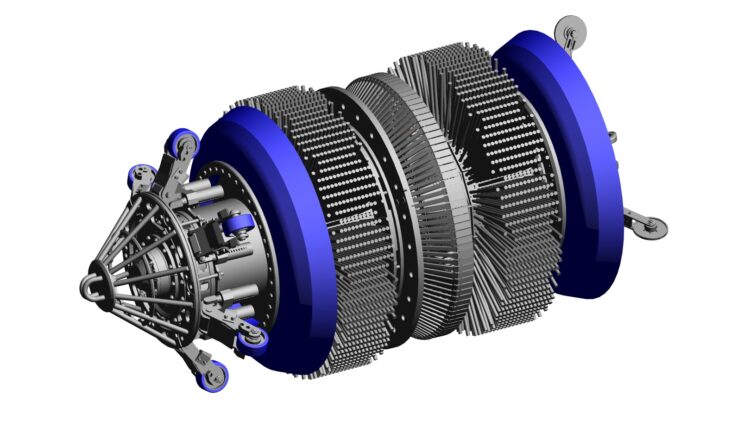
Source: transneft.ru
To identify defects in the pipeline, experts rely on the magnetic flux leakages signals. They differ in characteristics. Through the two main methods that use pattern matching and iterative approach, defects can be identified easily. Taking the measurements for repair or replacement also becomes more precise. Through various statistical data from set parameters, ground marking and artificial intelligence work from MFL-PIGs analysis and recommendations reports are easy to prepare. Experts will also give evaluations and predict future defect areas. Through pipeline inspection reports, operators can use them to enhance their adherence to the pipeline integrity regulations.
Natural gas and petroleum products are raw materials for various industries and a great source of energy. Maintaining the integrity of the pipelines as per the regulations is vital for environmental safety. MFL testing technique is more popular with pipeline inspection authorities because it uses numerical calculations to back up the theoretical research. It also establishes a clear relationship between the defect shape and leakage magnetic field for better defect analysis. Pipeline inspection technology keeps evolving due to advancements in technology. Future developments are likely to include robotic inspection tools and UAV technology implementation.