As the world progresses into the future, there is a dire need for electronics. Electronic components, machines, devices, and appliances are all a part of daily human life. Since these items typically involve the use of electricity, they do pose some threat to life and property if they are defective or are used improperly. In order to protect users from any damage, there are specific health regulations that every appliance needs to follow. Safety regulations basically lay down a guideline that would render an appliance fit for the market only if it fulfills them.
Page Contents
What Is PAT Testing?
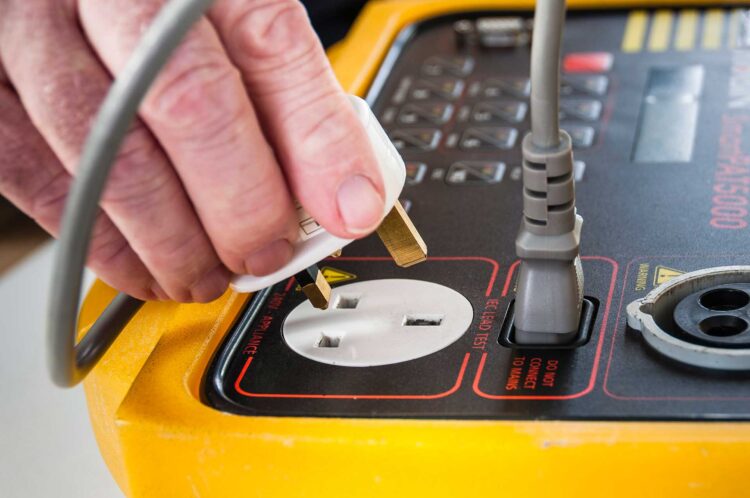
Source: bradwellmaintenance.co.uk
PAT Testing is an acronym for Portable Appliance Testing. The process involves multiple layers of inspecting and using an electrical component or appliance to adjudge whether the appliance is suitable for use by the public or not. The same testing is also necessary for industrial grade appliances. This form of testing is done on a healthily regular time frame so that all the batches are considered safe.
What Are the Requirements for Safety?
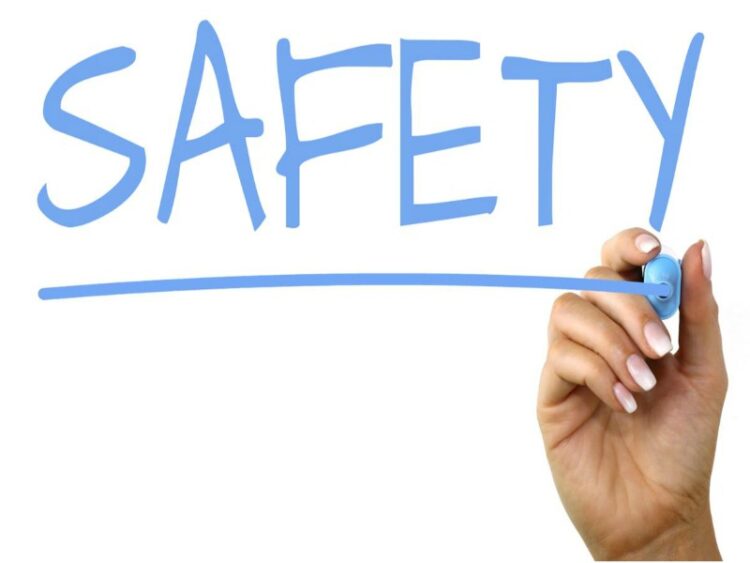
Source: miningreview.com
There are various parameters in electrical appliance safety. These minimum requirements aid the testing process by giving it a basis for comparison with standards.
Outer Controls
External controls of the appliance must not be complicated or ambiguous. An ambiguous control system will suggest that users may not really know how to operate the device. This kind of requirement is explicitly stated for household appliances as people would not have the training to operate them. Industrial devices can have slightly complicated controls on the ground that their uses and functions are complicated.
Only a trained person is supposed to operate such machinery. On the other hand, the controls should have proper labeling or icons to indicate the use of the buttons.
Apart from the essential requirement of keeping the external controls simple, there are some functional benefits that appliances must have as well. The buttons and controls should not be fixed in a way that the internal circuits are exposed to water, air, and dust. Preventing such gaps will ensure that even if the person is using the controls with wet hands, there will be no short circuit.
Component Protection
Components may have to be used in extreme weather conditions. These appliances may be stationed outdoors or indoors. Sometimes some components are exposed to high levels of heat from the sun or heat waves. There can also be heavy rain in thunderstorms or snow.
These weather conditions always have an adverse impact on all the components within an electrical device. If there is a device that is meant to be used in certain conditions, it should have the ability to sustain its operations in it. There should be no leakage into the device in any form. The machine should also not get overheated.
For example, computers have a built-in fail safe that allows them to cut power supply the moment it crosses the maximum acceptable temperature. The CPU temperatures are not meant to be too high, but sometimes due to the weather, they may possibly reach those extreme temperatures.
Dust Protection
There is a certain level of dust protection standard which must be followed. Ordinary machines will slow down and heat up when they are exposed to dust over the years. This not only harms the machine components but also raises the temperature of the operation. This can be highly dangerous to any individual who uses it or is around it.
An overheating appliance may as well reach such high temperatures that it starts a fire. Therefore, to prevent damage to both the appliance itself and the place of installation, it is necessary that there is dust protection in the device. If dust is inevitable, there should be appropriate claiming measures, whether manual or automatic.
Steps of Portable Appliance Testing
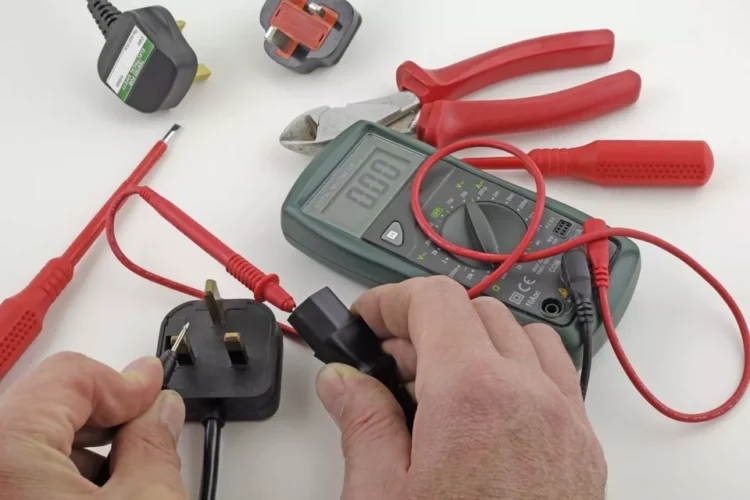
Source: phscompliance.co.uk
User Tests
The first step involves the basic steps of checking the device from the users’ perspective. This step generally emphasizes on the perception and use of the general users. The physical use of the appliance as the target consumer will provide the proper judgment as to whether the device is even applicable in regular use.
This step is considered one of the most important ones, as devices that do not pass the general user test will not be tested further. This is considered an informal testing procedure and is usually on the initial level of production.
Formal Checks
The next step involves an entirely formal test which involves a basic visual inspection of all the components by a specialist. The auditor will not only look at the device but also touch the device components to ensure that there are no loose ends in the product. If there are some basic faults, they can be eliminated. Further testing will not even be required. Further testing works when the device is able to hold well, even during the inspection.
Formal Physical Testing
The last step is to physically check the device by using it rigorously. It almost provides the limits to which it can function. Sometimes the testing procedure is such that it can provide various different ratings to the device. For example, the device may be safe for general use but has a fragile level of extremity. It can only function in suitable conditions and is not supposed to be used outside that. These devices are rated lower. Meanwhile, others are rated higher.
Conclusion
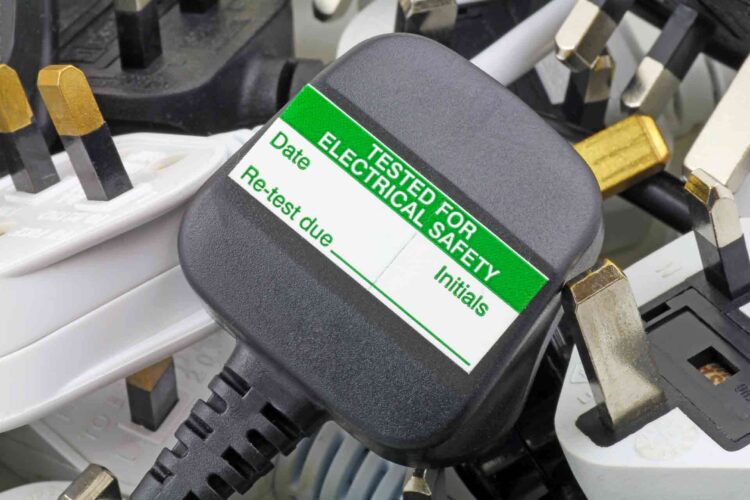
Source: checkatrade.com
It is really important for devices to comply with the safety standards to minimize harm to life and property. Since PAT provides an excellent basis to judge performance, PAT becomes a way to compare it with the standards set by regulatory authorities too. Testing is an essential aspect of the health and safety procedures.