Generator failures can strike at the worst possible moments, leaving you without power and facing hefty repair bills. A single major generator breakdown can cost anywhere from $5,000 to $20,000, a significant hit to any budget.
Understanding the common causes of generator failure isn’t just about preventing inconvenience but protecting your investment. These critical power systems require regular attention and maintenance to perform reliably when you need them most.
Here are the eleven key issues that can lead to generator failure. If left unchecked, each of these problems can escalate from a minor issue to a major failure.
Page Contents
Battery Failure
Battery failure is the leading cause of generator problems. A weak or dead battery stops your generator from starting when you need it the most, making you vulnerable during power outages.
Signs of Battery Problems
- Slow cranking during startup
- Clicking sounds when trying to start
- Complete failure to turn over
- Corroded battery terminals
- Bulging battery case
You can maintain and extend the life of your generator battery by:
- Conduction regular battery inspections, which involve voltage testing (12.6V is ideal)
- Load testing every 3 months
- Terminal cleaning and tightening
- Electrolyte level checks in non-sealed batteries
- Conducting an assessment of the physical damage
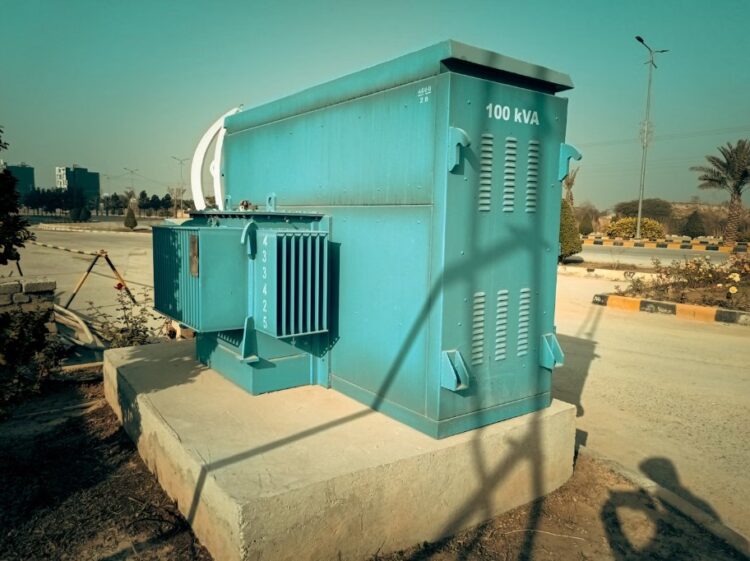
Source: unsplash.com
Fuel Depletion
Running out of fuel can trigger immediate generator shutdown and potential system damage. A dry fuel system requires professional bleeding to remove air pockets, leading to costly repairs and extended downtime.
You should set up fuel monitoring practices to prevent your generator from running out of fuel. You can do this by:
- Installing automated fuel monitoring systems
- Checking fuel levels weekly
- Tracking and documenting fuel consumption patterns
- Setting minimum fuel level alerts
You should also ensure the quality of the fuel by storing it in clean, water-free tanks. Test fuel quality every six months and add fuel stabilizers for long-term storage.
Air in Fuel System
Air getting into your generator’s fuel system can cause blockages that stop fuel from flowing properly. Air can enter your fuel system through:
- Loose connections in the fuel line
- Cracks in the fuel lines
- Seals or O-rings that aren’t working
- Empty fuel tanks
The telltale signs of air in the fuel system are when:
- The engine is sputtering
- It’s hard to start the generator
- The generator shuts down unexpectedly
- The engine is running unevenly
Follow these steps to get rid of air in your generator’s fuel system
- Find the fuel bleed screw on your generator
- Put a container underneath the bleed point
- Slowly loosen the bleed screw
- Let the fuel pump run until you see clear fuel flowing
- Tighten the bleed screw back up
- Start the generator and check if it’s running properly
- Regularly checking your fuel lines and connections can prevent air from entering the fuel system.
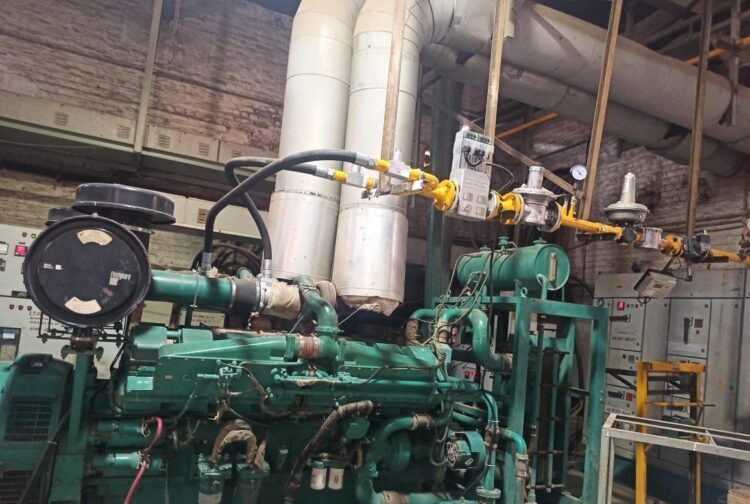
Source: indiamart.com
Stator and Rotor Failures
Stator and rotor failures are serious problems with generators that require expert help. The stator is a stationary part that holds the electrical windings. It works together with the rotor to produce electricity using electromagnetic induction.
Common signs of stator and rotor failures include:
- A burning smell from the generator
- Unusual noise during operation
- Reduced power output
- Inconsistent voltage readings
- Excessive heat generation
The leading causes of the failure include insulation breakdown, bearing wear, which affects rotor alignment, electrical shorts in windings, moisture infiltration, and physical damage from debris.
These complex issues require professional diagnosis and repair. Trying to fix them yourself can cause permanent damage and expensive replacements. If you do need to replace your generator, find a local expert. Whether you want Generac Generators in St Louis or Billings, check reviews and testimonials online before hiring one.
Accidental Activation of Emergency Stop
The emergency stop button is an important safety feature in all aspects. In generators, it allows for immediate shutdown in dangerous situations. However, this red mushroom-shaped button can be accidentally activated, leading to unexpected operational stops.
What are the common causes of accidental activation?
- Maintenance personnel accidentally press the button during routine inspections.
- Objects falling against the control panel and triggering the button
- Children or unauthorized individuals gaining access to the generator area and tampering with the button
- Weather conditions cause debris to hit the button and activate it
If the emergency stop button has been unintentionally activated, follow these troubleshooting steps:
- Check the surrounding area for any potential hazards that may have caused the activation
- Inspect the button itself to ensure it is not damaged or stuck in the pressed position
- Turn the button clockwise to release it from the locked position
- Reset the generator’s control panel according to the manufacturer’s instructions
- Verify all safety parameters before attempting to restart the generator
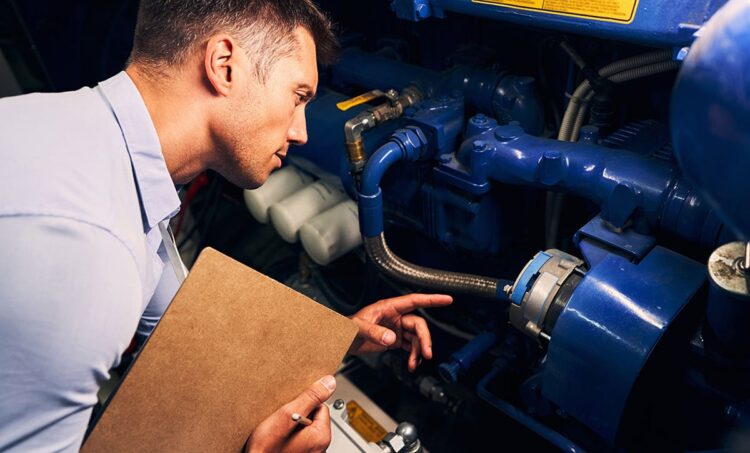
Source: kohler-ups.co.uk
Clogged Air Intake
A clogged air intake can bring your generator to a grinding halt. Dirt, debris, and other contaminants restrict airflow to the engine, creating serious combustion issues that affect your generator’s performance.
Warning Signs of Air Intake Blockage
- Excessive black exhaust smoke
- Reduced power output
- Unusual engine sounds
- Higher fuel consumption
- Frequent shutdowns
You can clean air intake blockage by:
- Powering down your generator
- Locating the air intake filter
- Removing the filter housing
- Inspecting for visible debris
- Cleaning with compressed air
- Replacing the air intake filter if it is damaged
Carbonization
Carbonization occurs when your generator runs at low loads for extended periods. Unburned fuel creates carbon deposits in the engine’s combustion chamber, valves, and exhaust system during this process.
This impairs the generator’s performance by:
- Reducing engine efficiency
- Increasing fuel consumption
- Higher maintenance costs
- Potentially causing engine damage
- Shortening your generator lifespan
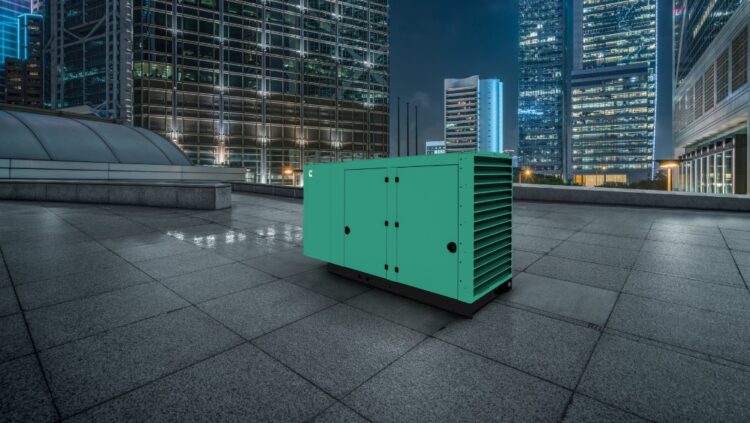
Source: cummins.com
Circuit Breaker or Fuse Issues
Circuit breakers and fuses are essential safety parts of your generator system. They prevent damage to your generator. Here are some common signs that there might be a problem with your breaker or fuse:
- Sudden power loss while the generator is running
- Generator not starting
- Burning smell near electrical parts
- Visible damage or discoloration on fuses
To ensure the safety of the circuit breakers and fuses, turn off all power sources when the generator is not in use. Use insulated tools during maintenance, test circuits with a multimeter before touching, and wear appropriate protective gear.
Alarm Faults
Alarm systems are your first line of defense against potential damage to your property or harm to people. These advanced monitoring systems track critical parameters and notify you of any abnormal conditions before they become expensive repairs.
Your generator alarm will ring to signify the following:
- Low oil pressure warnings
- High-temperature indicators
- Low fuel level alerts
- Battery voltage irregularities
- Start failure notifications
It’s wise to note that each alarm type signals specific risks to your generator’s operation:
- Red alerts require immediate shutdown
- Yellow warnings indicate potential issues
- White notifications suggest maintenance
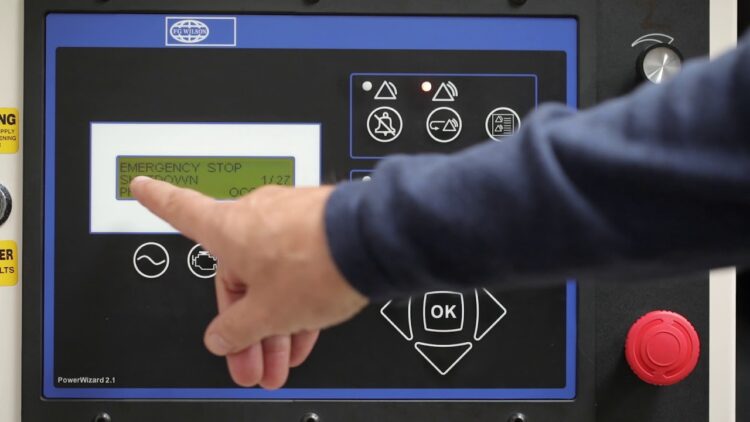
Source: my.fgwilson.com
Cooling System Failures
Your generator’s cooling system is critical in maintaining optimal operating temperatures. When coolant levels drop or the system malfunctions, your generator faces serious risks of overheating and potential engine damage.
The critical warning signs include:
- Unusual engine noises
- Steam from the engine compartment
- High-temperature gauge readings
- Automatic shutdown during operation
Maintenance practices include:
- Check coolant levels weekly
- Inspect hoses for leaks or damage
- Clean radiator fins to prevent blockage
- Test coolant concentration every 6 months
Mechanical Vibrations and Bearing Failures
Mechanical vibrations can significantly impact your generator’s performance and lifespan. These vibrations are often caused by:
- Misaligned components
- Loose mounting bolts
- Unbalanced rotors
- Worn-out bearings
Generator bearings support the generator by ensuring smooth rotation while reducing friction. When bearings fail, you may experience unusual noise levels, excessive heat generation, reduced generator efficiency, and metal-on-metal grinding sounds.
Implement the following measures:
- Install vibration dampeners
- Conduct regular alignment checks
- Implement proper lubrication schedules
- Monitor bearing temperature
- Schedule periodic vibration analysis
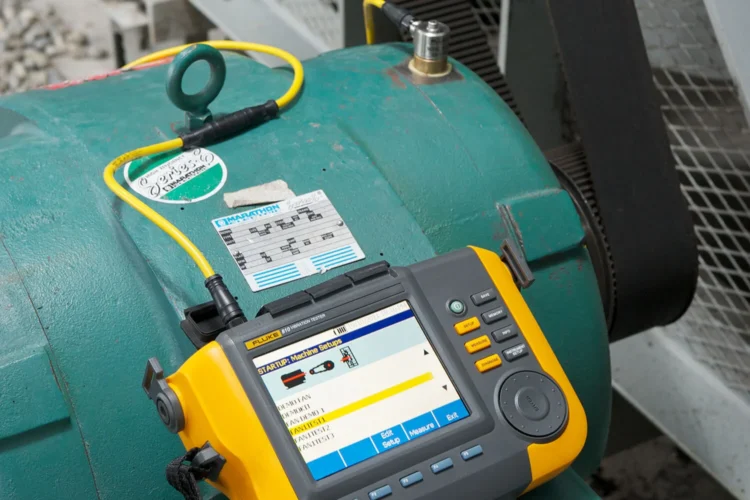
Source: fluke.com
Final Thoughts
Failure in your generator can cause significant losses in your home and business. In the discussion above, we’ve addressed the eleven leading causes of generator failure, cause, and how to ensure the smooth running of your generator, with the most prominent point being regular maintenance.